Stamping Die Spotting Machine ST Series
SpreX- 100ST/300ST
Innovatively use the impact force of falling body instead of the static pressure mold closing force of the conventional die spotting machine to realize the inspection function. The moving and fixed molds have a very large impact force at the moment of free fall contact, so the single printing effect is better than that of the conventional die spotting machine with the same mold surface slze.
High-standard configuration and computer-aided design ensure the excellent performance of the machine. The main machining parts are all processed by imported machining centers to ensure the processing accuracy of mechanical parts, and the related heat treatment of important parts and materials that are easy to wear parts improve performance. The hydraulic system adopts the optimized combination of high-performance imported hydraulic parts, and the control part adopts the computer control system of special die spotting machine.
Design Focus
- With the same mold size equipment, the overall dimension of stamping mold closing machine is about 25% smaller than that of traditional mold closing machine, and the utilization rate of workshop is higher
- Hidden oil tank and motor make the overall appearance simple and beautiful
- Reinforced high rigid base ensures overall rigidity of equipment under high impact force
- Practical and reliable fault detection and alarm functions
- The oil-free and self-lubricating graphite copper sleeve guide makes the machine cleaner and environmentally friendly; low friction coefficient with no "adhesion" phenomenon
- Mechanical, electrical and hydraulic measures are available to ensure consistent rotation reset positions
- The oil-free and self-lubricating graphite copper sleeve guide makes the machine cleaner and environmentally friendly; low friction coefficient with no "adhesion" phenomenon
Choose Your Model
Related Applications
SpreX's products have a wide range of applications, including plastic molds, die casting molds,stamping molds, injection molds, creating more value space for customers.
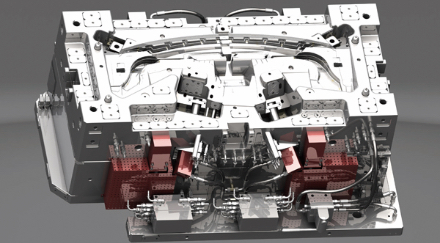
Injection Molding
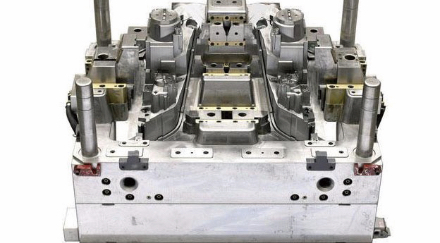
Die Casting
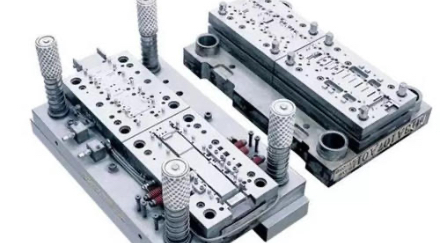
Stamping
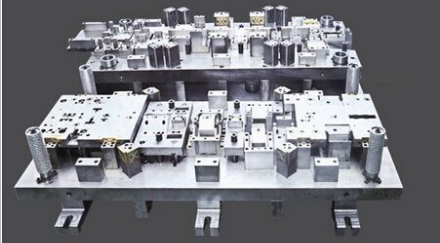
Stamping
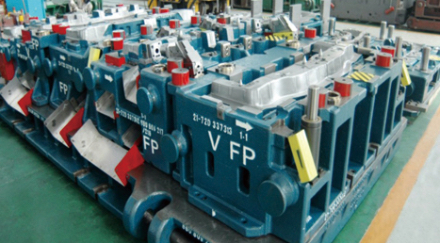
Stamping
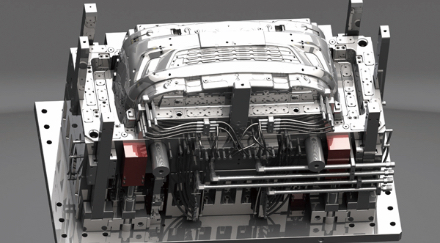